Currently in refineries, the gasoline blending scheduling problem is largely dependent on manual scheduling, and existing research results have not been well applied in actual production.
The team of Associate Professor Du Wei from East China University of Science and Technology, through communication with refinery schedulers, believes that the main reason is that existing optimization methods require re-setting of parameters, strategies, etc., when production process conditions change. These tedious tasks greatly reduce the enthusiasm of schedulers to use optimization algorithms.
Therefore, in a recent study, Du Wei and his team hope to combine diffusion models and multi-objective optimization techniques to solve industrial process scheduling optimization problems.
The main purpose of gasoline blending is to start from the perspective of existing resources in refineries, comprehensively consider the blending capacity of refining enterprises, market demand for products, and product indicators, and optimize the inventory of component oil and finished oil as much as possible, while meeting the upper-level demand plan, to maximize the economic benefits of the refinery.
Advertisement
The problem faces challenges such as large scale, a large number of constraints, mixed integers, and non-linearity. Previous studies have focused on reducing the complexity of the problem on the modeling side, so that existing optimizers can solve it.However, these methods that make additional assumptions about the problem largely limit the upper limit of the final solution, and these assumptions are usually based on specific working conditions. Once applied to different scales, different raw materials, and different pipeline structures, the entire method needs to be redone from the modeling level.
This undoubtedly is not conducive to the universality of the designed method, which also leads to the current actual industrial site, dispatchers often rely on manual experience to carry out the work of gasoline blending scheduling.
Therefore, this study attempts to effectively solve the gasoline blending scheduling problem that fits the actual industrial application scenario. However, the past methods, whether based on the mathematical programming optimizer of traditional operations research or the evolutionary algorithm based on stochastic optimization that has risen in recent years, are difficult to effectively solve the mixed integer optimization problem with a large scale and a large number of constraints.
Therefore, it is necessary to use a new method that is fundamentally different in principle. This study, through the proposed method - the Multiobjective Optimization based on Diffusion Model (DMO), cleverly introduces the representative model of the image generation field, the diffusion model, into the field of scheduling optimization by using the property that "the Gantt chart of the scheduling process is an image."
The research team uses the diffusion model to learn the distribution of historical operation data, and obtains the final solution through iteration with the assistance of the target gradient.The experimental results show that DMO not only enhances the production efficiency of the refining process but also reduces costs and improves product quality, filling the gaps in previous research and providing a completely new perspective for industrial scheduling optimization.
DMO starts from the original form of the problem, relying solely on historical operating data, which is very easy for factories to obtain. Therefore, the use of DMO does not add extra burden to schedulers.
At the same time, DMO operates very efficiently, allowing schedulers to try repeatedly, thus reducing the time cost of learning this tool.
In the initial stage of DMO application, schedulers can use the optimal solutions generated by DMO as a reference to assist manual scheduling, and eventually transition to solving problems using algorithms.
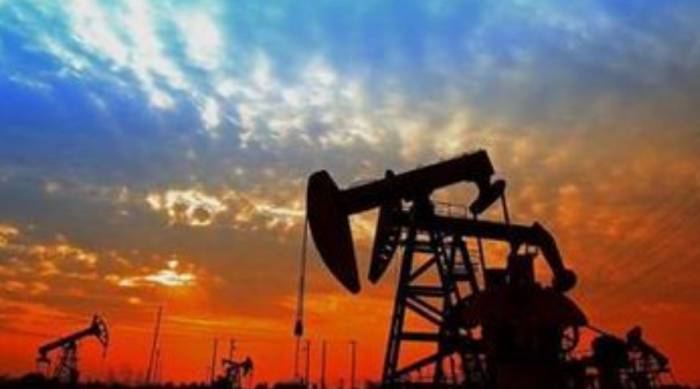
Therefore, in the gasoline blending scheduling problem, DMO overcomes the shortcomings of previous methods, making it widely applicable in actual production.For other application scenarios, the research group believes:
Firstly, DMO also has tremendous potential in other production processes of the refinery, such as crude oil scheduling, etc., which have similar characteristics to gasoline blending scheduling.
Secondly, they believe that DMO also has great potential in product design problems, which usually have a large number of optimization parameters, complex constraints, and multiple objectives. DMO can generate a large number of solutions with different characteristics, and even if these solutions cannot be truly practical, they can still help and inspire designers to carry out further design.
In fact, in their previous work, the research group has conducted a lot of research on the gasoline blending scheduling problem and has communicated with the refinery schedulers many times.
They have a specific understanding of the characteristics of the problem and the shortcomings of existing methods, and they realize that if the algorithm is to have application value, it needs to follow the following two points:Firstly, modeling should be conducted as closely as possible to the original data to ensure the applicability of the algorithm;
Secondly, the external environment of the refinery is variable, and its trade-off between loss and efficiency is not immutable, hence it should be regarded as a multi-objective problem.
The former will lead to a large number of decision variables and constraints, while the latter requires the generation of a large number of solutions to form a Pareto front in one go, which increases the complexity of the problem far beyond the capabilities of traditional optimization algorithms and evolutionary algorithms, thus they need to find a new method.
They have noticed that in recent years, diffusion models have begun to rise in the field of image generation, quickly overwhelming the widely used generative models before - Generative Adversarial Networks (GAN).
On the one hand, diffusion models can handle a large number of parameters such as image pixels, and on the other hand, the batch-based usage in deep learning can generate a large number of solutions at the same time, which meets the two requirements mentioned above.And more critically, the iterative nature of diffusion models is a disadvantage in the field of image generation, which means consuming a large amount of computing power and a longer computing time.
However, in the field of optimization, this process can easily be linked to the iteration in optimization algorithms. The solutions in the same batch are like a population in evolutionary algorithms, and the diffusion model iterates the solution each time, just like the mutation operation in evolutionary algorithms.
This similarity led them to apply diffusion models to the optimization of gasoline blending scheduling problems.
Since applying diffusion models to optimization problems is a brand new attempt, there is no existing work to refer to.
At the same time, research on diffusion models in the field of image generation also focuses on reducing the amount of computation and enriching the content of generation, which cannot be directly used in the field of optimization. Therefore, "from scratch" to carry out this research faces many difficulties.In their research, they referred to the early architecture of the diffusion model, which involves using an independent discriminator to assist in generating specified content and replacing the discriminator with an objective function.
After the framework was constructed, there were still many choices to be made, such as whether to use a CNN or a Transformer for the network? How to design the weights between objectives? How to implement multi-objective optimization? And whether to incorporate a selection mechanism?
After repeated experiments, they decided on the current DMO method. Ultimately, the experimental results confirmed that their intuition was accurate, and the DMO had significant advantages compared to the comparative algorithms.
Du Wei said, "The collaborators on this project include Academician of the European Academy of Sciences, IEEE Fellow, Professor Jin Yaochu from Westlake University, IEEE Fellow, Professor Gary G. Yen from Oklahoma State University in the United States, and IEEE Fellow, Professor Tang Yang from East China University of Science and Technology."
They are all authoritative scholars in the field of artificial intelligence. When Du Wei first discussed the idea with them, they all found the idea very interesting, especially the clever introduction of the diffusion model, a generative model technique, into the solution of scheduling optimization problems by utilizing the fact that "a Gantt chart is an image."This has greatly encouraged Du Wei and his team, making them realize that their research work is at the forefront of international academia.
Recently, the related paper was published under the title "Diffusion Model-Based Multiobjective Optimization for Gasoline Blending Scheduling" in IEEE Computational Intelligence Magazine (DOI: 10.1109/MCI.2024.3363980).
Master's student Fang Wenxuan is the first author, and Du Wei serves as the corresponding author[1].
In subsequent research, they plan to combine more actual production data and experimental results to verify and refine the methods they proposed. In addition, they will also explore the potential for applying this method in other industrial processes, using it for completely different types of optimization problems, such as combinatorial optimization problems, etc.
Comment